CERMET has key core production experience throughout PIM manufacturing.
Customised delivery
From the production of raw material powders, the prediction of product quality and its precise assessment comes from more than ten years of experience in the original production of gold ceramics.
Wide compatibility
Let feedstocks that is to serve the product, but also the different forms and sizes of the product.
No worries about production
Feeding from the beginning of delivery to the end of production, no need to worry about problems, we come to the decision-making solution. Don't know the production process parameters? We deliver them attached to your order!
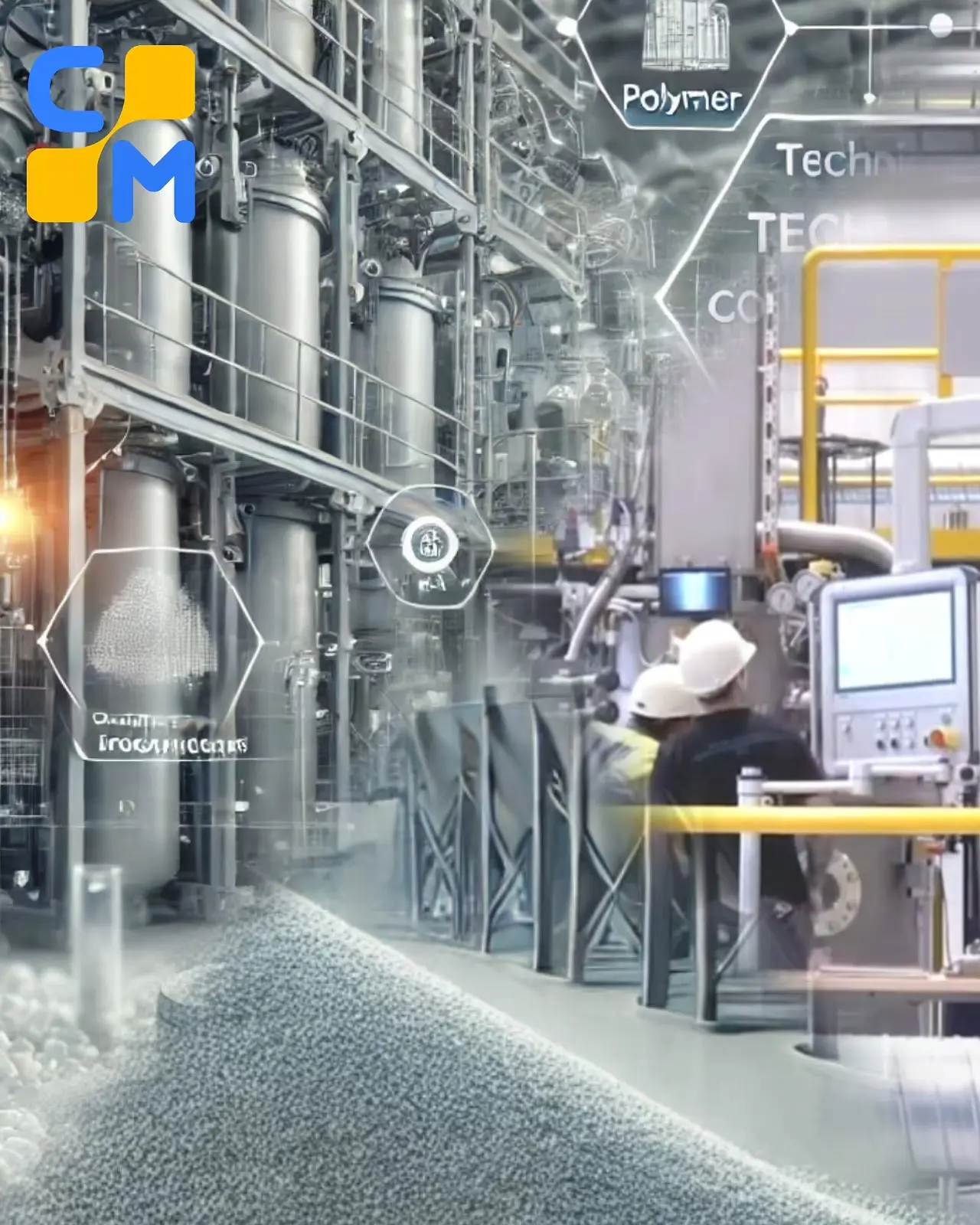
High-quality adhesives developed and manufactured in-house
We have cooperated with material companies for many years and independently developed and produced modified acrylic ceramic binder, which is specially used in CIM ceramic injection moulding formulations, suitable for the development and manufacture of different advanced ceramic material feeding products, and can be used in zirconia, alumina and other ceramic materials. Modified acrylic is a special material for CIM binder formulations for injection moulding of nano-sized ceramic powders, which is made of curing agents, accelerators, dispersants, stabilisers, toughness agents, and modified with a variety of polymers and special additives.
Binder polymer ratio in the application of powder injection moulding technology (Powder Injection Molding, PIM) occupies a core position, all of our company's binder are their own exclusive R & D and production, according to the equipment and product requirements of different manufacturers, tailored to a variety of binder formulations system of acid degreasing, thermal degreasing, solvent degreasing, and other customised feeding. Our binder has excellent powder affinity, strong adhesion to powder, excellent adhesion to ceramic powder, can effectively prevent powder agglomeration and segregation, prevent uneven distribution and product cracks; low contact angle, no deformation and no broken material, to ensure the stability of product size.
Binder degreasing rate is high, low ash content, degreasing thoroughly without residue, degreasing temperature interval is wide, suitable for a variety of degreasing process; ultra-high mobility, uniformly fill the gap between the powder, reduce the surface of the product flow pattern, increase the brightness of the product to eliminate the surface matte. And compatible with a variety of binder formula elements, a variety of high and low molecular binder adaptable range, matching the ceramic thermal expansion coefficient, a wide range of compatibility for a variety of particle size range of ceramic powder; curing shrinkage is small as well as ultra-high strength and toughness, many times the repeated processing and cyclic heating.
Refined Expertise Innovative Excellence

Control of feed quality from material production
Kincera Feeding Technology also works with powder producers on a deeply customised basis. The end-use quality of many materials is related not only to the feed, but also to the material science properties of the powder. For example, titanium alloy powders are produced using a technology that focuses on vacuum induction droplets, and the powder supplier that works with Kincera has shown a very impressive photo of a vacuum droplet from this aerosolised production system. Titanium powder manufacturing typically involves both aerosolised and water atomised production methods, which involves bombarding the powder with a high velocity argon gas stream and cooling it down underneath the equipment through a filtration and layering system, and fine screening for particle size.
The droplet frequency and flow rate, gas flow rate, gas dynamics and circuits are very critical to the morphology and quality of the powder, which have a non-negligible impact on the final quality of the product, and we have started to control the quality of the fed product from here on. We have deep cooperation and communication with powder material manufacturers, in order to intervene technically in the manufacturing process of the material front-end, and to analyse and adjust the mechanical properties, salt spray test, electromagnetic properties, and appearance requirements of the final product, so as to solve the problems and defects of the product (or non-standard product) from the source.
Copyright © 2024.Dongguan Cermet Technology CO.,LTD All rights reserved.
粤ICP备2024252432号